e—メタン試験施設をスケールアップ カーボンニュートラル化へ前進
構成部材の高度化にも力 独自触媒でコスト低減へ
装置だけでなく、構成部材の高度化にも力を入れている。特に注力しているのがSOECセルの改良だ。現段階では「セラミックス支持型」を採用しているが、これには、強度不足や大型化が難しいといった課題がある。そこで、セラミックス板の代わりに金属板を用いた「金属支持型」セルを開発。強度が増し、構造のコンパクト化が図れる上、溶接が可能で、低コストでの大型化が容易といった利点がある。この新型セルはラボスケールでの検証を終えており、27年度にベンチスケールでの試験を開始する予定だ。
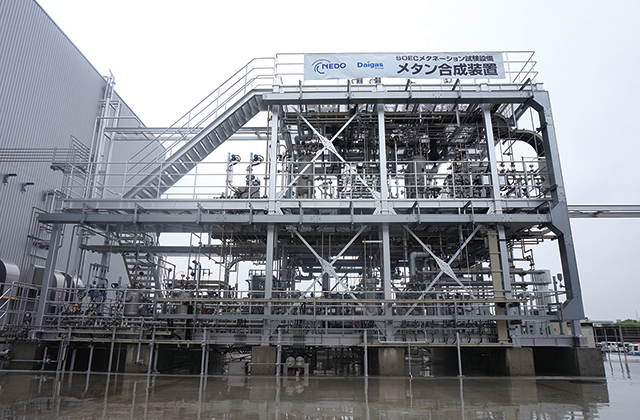
他方、メタン合成反応は、温度が低いほどメタン生成濃度を高められる半面、反応速度が低下するため触媒の量を増やす必要があった。そこで、代替天然ガスや燃料電池の開発などで培った触媒技術を生かし、より低温で高いメタン生成速度を有する触媒を開発。これにより、メタンの生成濃度を高めながら反応器を小型化することが可能になり、さらなるe―メタンの製造コスト低減が期待できる。
藤原正隆社長は竣工式で、「SOECメタネーションには、まだ取り組むべき技術的課題があるものの、実現すればe―メタンの低コスト化・普及を加速させる大きな可能性を秘めている。ベンチスケールでの試験を始められたことは、カーボンニュートラル化に向けた大きな一歩だ」とその意義を強調した。
今回完成した試験施設は、かつて石炭から都市ガスを製造していた酉島工場の跡地に立地する。往年のエネルギー供給拠点が、まさに今、脱炭素時代の最前線を走る研究施設として生まれ変わろうとしている―。
1 2